Hempcrete is used as a highly insulative wall material. It is a carbon-negative, natural, and lightweight construction material that provides highly efficient temperature and moisture control. It is also formable, dynamic, one-seventh the weight of concrete, and cures within hours.
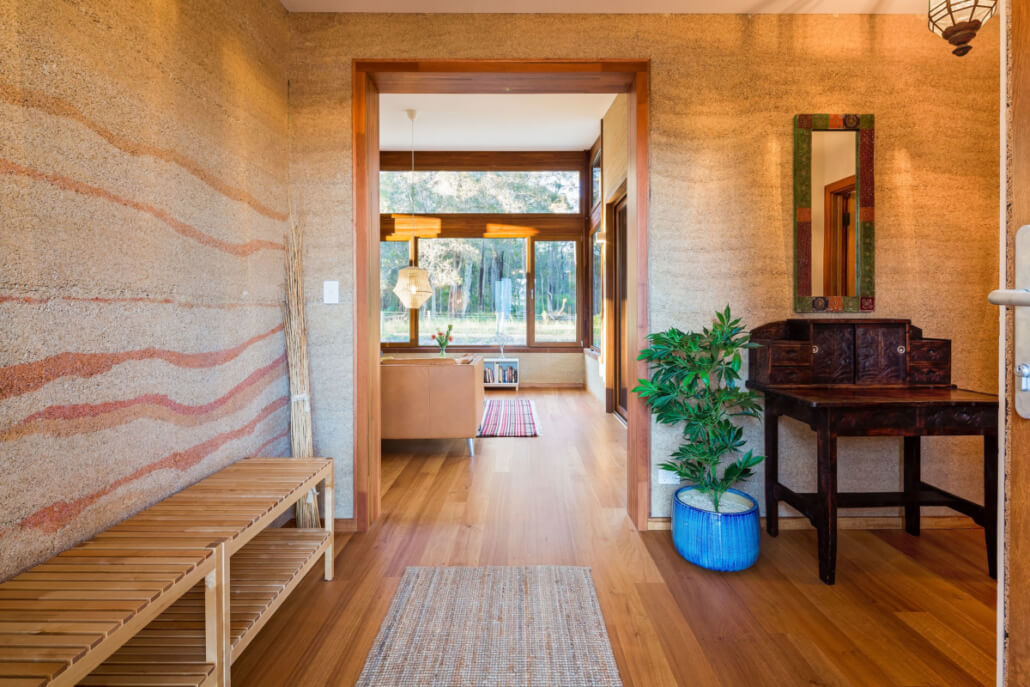
What Are the Benefits of Hempcrete?
The benefits are manifold. It is highly insulative, regulates humidity to safeguard against asthma, is fire resistant, termite resistant, rodent-proof, and prevents mold and rising damp. It never rots. It preserves the timber house frame, generates zero landfill, sequesters carbon, and is nontoxic.
Related Post: Earth Sheltered Home: An Eco-Friendly, Passive Housing Alternative
What Is Hempcrete Made From?
Hempcrete is made by mixing the inner woody core of the stalk known as the hurd with a natural, lime-based binder, and water.
To separate the hemp fiber from the woody core, the plant stalk is left to rot (a process called retting) for 4 to 6 weeks. Microbes break down the pectin in the stalk to facilitate separation. After retting, stalks are dried and then passed through toothed rollers which crush and break the woody core into smaller pieces.
Hemp hurd is simply a byproduct of hemp fiber production. What was found (by the French) is that hemp hurd could be used as an aggregate for construction, and its addition dramatically improved — in several capacities which this article will endeavor to cover — the performance of the structure.
When and Where Did It Come From?
If youโve ever had the pleasure of traveling to France, you might have seen the many old, oak-frame colombage buildings. Between the oak, mixtures of lime, straw, rubble, sand, and clay are stuffed. No matter how hard you search online, you wonโt find the name of the genius who swapped out straw for hemp hurd. But since then — at some point in the 1980s — the idea spread across France, into the UK, and all through Europe. Today, there are thousands of hemp houses on every continent.
Is Hempcrete Better Than Concrete?
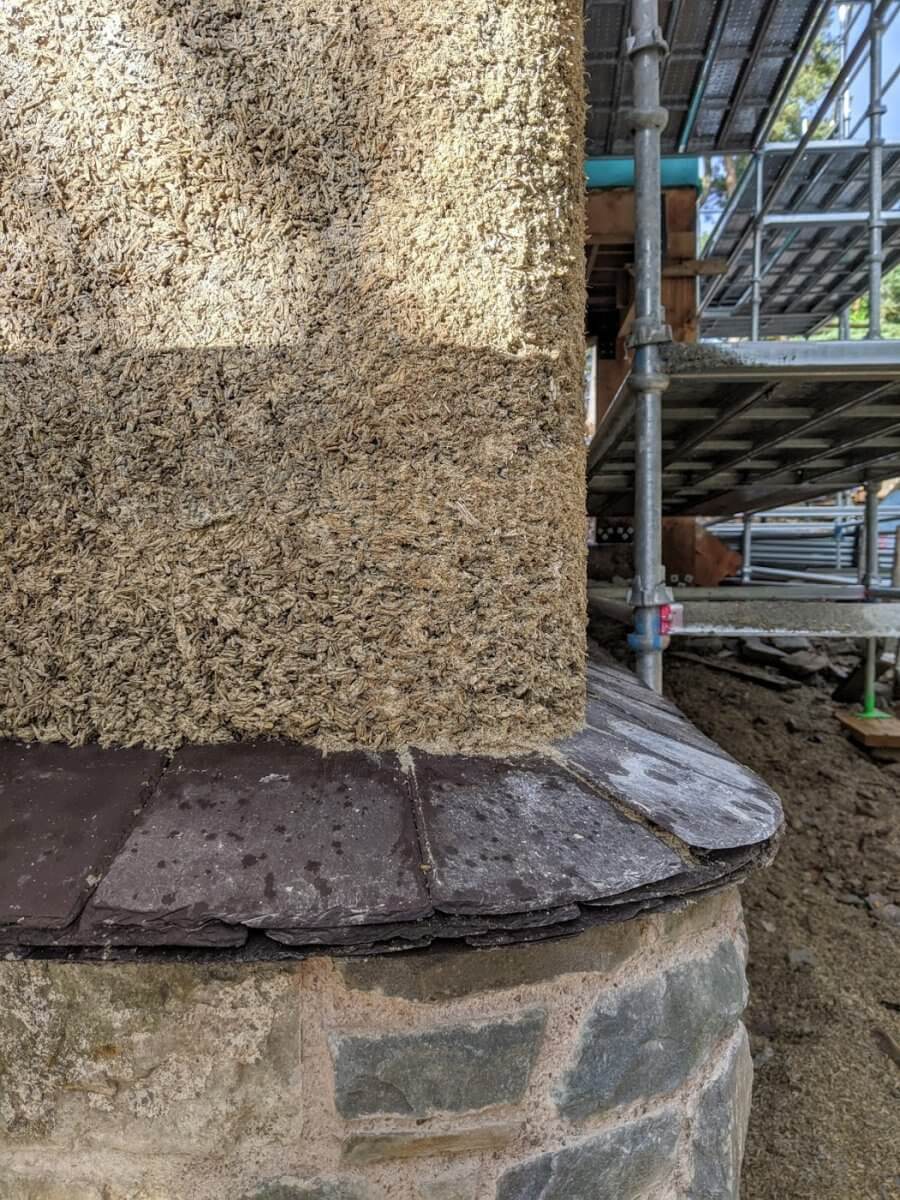
Hempcrete may be one of the most Googled phrases in the industry. Perhaps it was a mistake to fix “-crete” on the end of the word, because, even though it does roll off the tongue, hempcrete is very different from concrete.
Concrete is a material used to create foundations and load-bearing structures. It’s heavy, cold to the touch, and has zero insulative qualities.
Hempcrete, on the other hand, is super light. In fact, it is one-eighth the weight of concrete. It is non-load-bearing and best described as a masonry infill material with a porous, airy, fibrous composition. It is currently in the spotlight for several reasons: It’s a high-performance insulator, able to regulate the moisture content of the house (providing a sense of comfort and relief from allergies), and so eminently carbon-negative it can mitigate the carbon footprint of the entire house building process. For those who want to delve deeper into the building science behind the performance of hempcrete, Iโve written more extensively here.
What Is in Hempcrete and Can I Source It Myself?
Hempcrete has three constituent parts: hemp, lime, and water.
Hemp, and Where to Source It
Here in Australia, hemp shiv is only beginning to be farmed and brought to market. (A couple of notable enterprises being Hemp Homes Australia and X-Hemp in Tasmania where 80% of the hemp in Australia is currently farmed).
In Europe, a large industry is established and growing, with processing facilities in France, Holland, and Germany. The last house I built — working in Scotland — was made with Lithuanian hemp.
Over in the US, hemp production has exploded since the Agriculture Improvement Act or Farm Bill of 2018, finally allowing hemp cultivation after many, many years.
The Binder
As you might assume, the binder is what binds the hemp shiv into a solid mass. The binder consists of either hydrated lime or natural hydraulic lime. Hydrated lime (or air lime) has no impurities and is made by kiln-firing limestone. The firing process removes the carbon molecules from the limestone and converts it into a dry powder. When you want to use lime as a binder or mortar, you introduce carbon dioxide again, essentially converting the lime back into limestone as it absorbs surrounding CO2. This is what’s known as the carbon cycle.
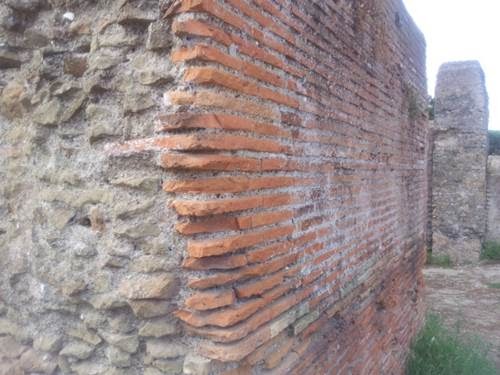
The other lime, hydraulic lime, is also kiln-fired using the same process. The difference being hydraulic lime has added or existing impurities known as pozzolans.
Why Add Impurities and Why Give Them Such an Exotic Name?
The addition of pozzolans causes lime to set in what’s known as a chemical set — whereby the lime returns to limestone in the presence of CO2 and water. This set is quicker and stronger. The set can also occur deeper in the hempcrete wall where an air or hydrated lime may not have an abundance of CO2 to set in a convenient time frame. And the name? Pozzolans were originally quarried by the Romans 2500 years ago in Pozzuoli, next to Naples, and under the watchful gaze of Vesuvius.
One tremendously interesting fact is that hemp hurd has a high silica content. And silica just so happens to also be a pozzolan. So the actual hemp itself serves not only as an insulative aggregate, but to increase the strength and set speed of the lime.
There are many benefits of using a natural lime mortar as opposed to modern portland cement. One only needs to look at the Colosseum or Pantheon to see the benefits of a binder that is more flexible and vapor open. This reason is one of many that natural builders are so passionate and vocal about their methods. Theyโre often preindustrial, tremendously reliable, have a fraction of the carbon footprint, and the buildings they build stand longer.
Lime is very common across the globe. Depending on your country, you may only be able to source either hydrated or hydraulic in their natural forms. But you can always add a pozzolan if needed.
Understanding lime is beyond the scope of this introduction as the chemistry and interactions between hemp and lime are complex (and tremendously interesting). Various lime choices exist and are on a sliding scale of sustainability and utility. Amusingly, lime is a contentious subject in the natural building community. Have a read here http://www.stastier.co.uk/nhl/topics/mineralogy.htm
How Is a Hemp House Built?
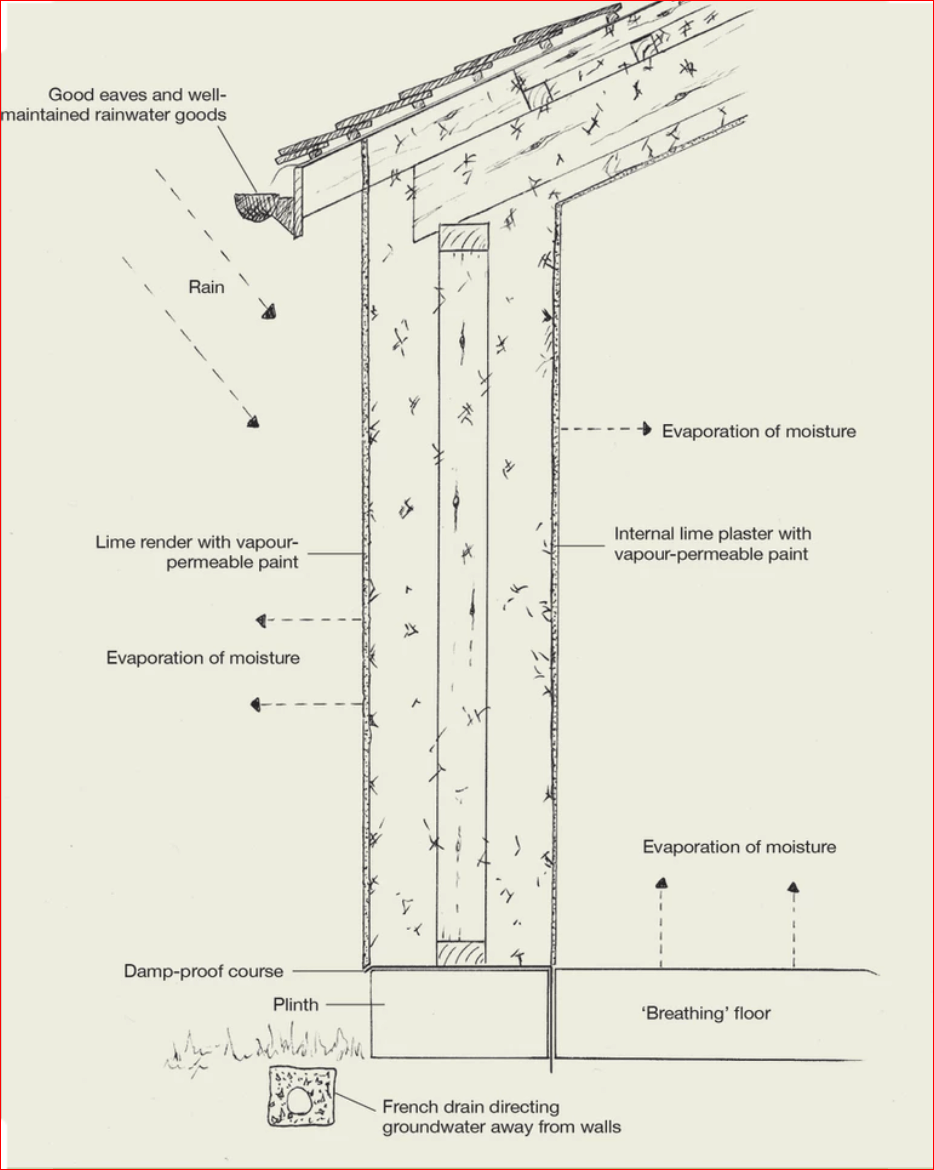
Hemp houses are often made using the standard timber stick frame that youโd see in a new build or renovation. The stick frame serves as the load bearer and skeleton which the hempcrete encases or shrouds. In the UK, studs are called out as 6-by-2 or around 150mm x 45mm. In Australia standard 90mm x 45mm studs are used and actually work to benefit a hempcrete build. This works because as hempcrete surrounds the frame, you want as much meat or expanse of hempcrete on each side of the stud — the wall mass to the inside of the wall and the wall mass to the outside — with the stud being in the center.
In other words, the more mass of hempcrete you have that is unbroken by timber stud work, the stronger the hempcrete, which is why you want the stud frame in the dead center of the wall detail. You generally want more than 80mm of hempcrete on either side of the stud frame which is easy to achieve as most hempcrete wall thicknesses are called out between 250mm to 400mm.
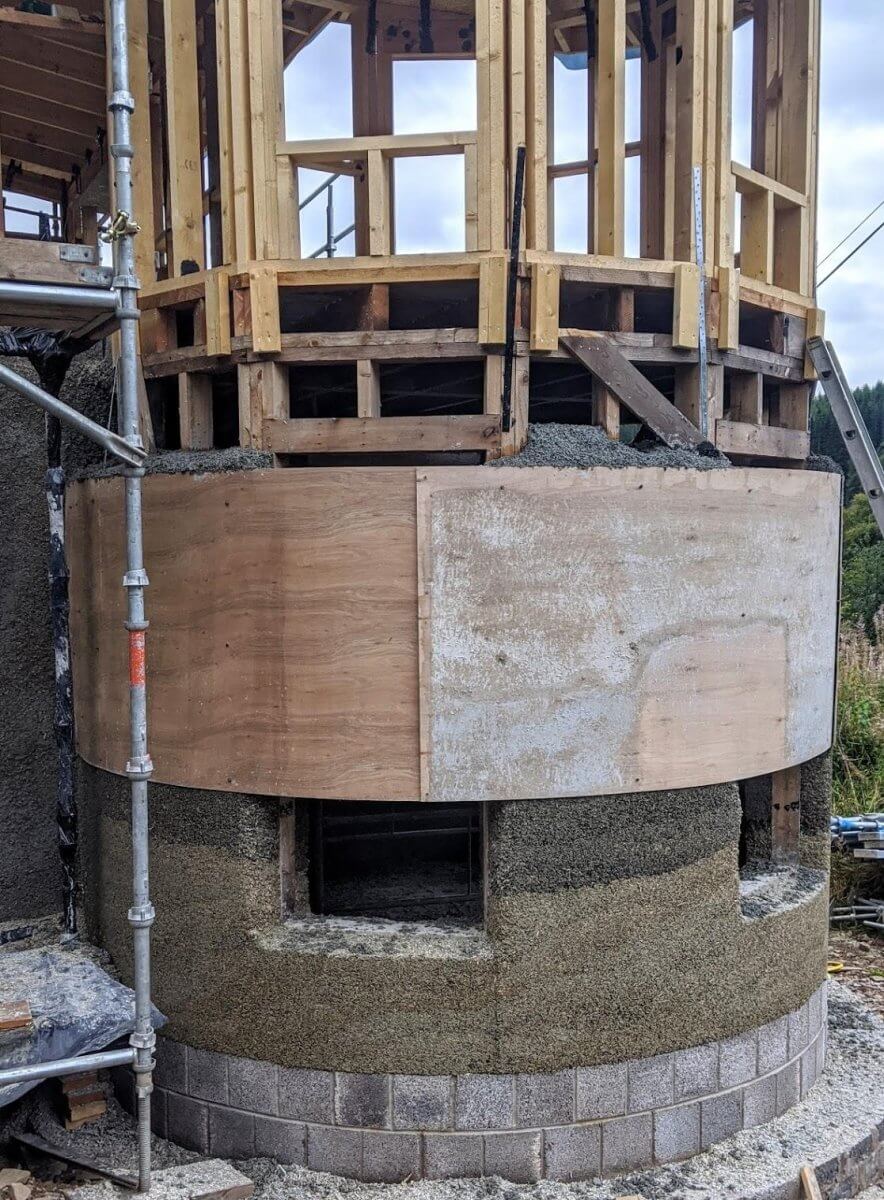
Formwork or Shuttered Hempcrete
The most common method of construction is to create formwork or shuttering and to pour the wet hempcrete mixture into the form from buckets. It has the lowest barrier of entry in terms of skill, and often homeworkers and the community can jump in and ferry buckets under the guidance of a skilled hempcrete contractor. The formwork itself doesnโt have to be super strong as it isnโt a liquid in its workable form. Hemp as a material has quite a lot of friction, so as it is poured into the forms it does not suffer droop. In fact, once poured, the outside edge of the wall is tamped to create more compression and solidity. The tamper job is a premium, sought after, and satisfying role on the hempcrete worksite.
Spraying Hempcrete
Here you can see the hempcrete sprayer in action.
This process is essentially run by two pumps: A conventional concrete pump for the lime, and a specialized, hemp dry pump (premixed hempcrete still hasn’t been successfully run through a single line as so much friction is encountered). The two are shot separately through the lance and converge on the wall with the lime binder battering and coating the hemp upon impact. This method is great for creating curves and infilling hard to hand-place spots, such as where the wall meets the ceiling or spots you might have missed during hand placing. Toward the end of this video, you can see how a horizontal batten is attached with the leading edge being the reference point for the finish line of the hempcrete. From this batten, a straight edge is hung, allowing the wall to be flattened, and shaving off high spots on the fly.
Hempcrete Blocks
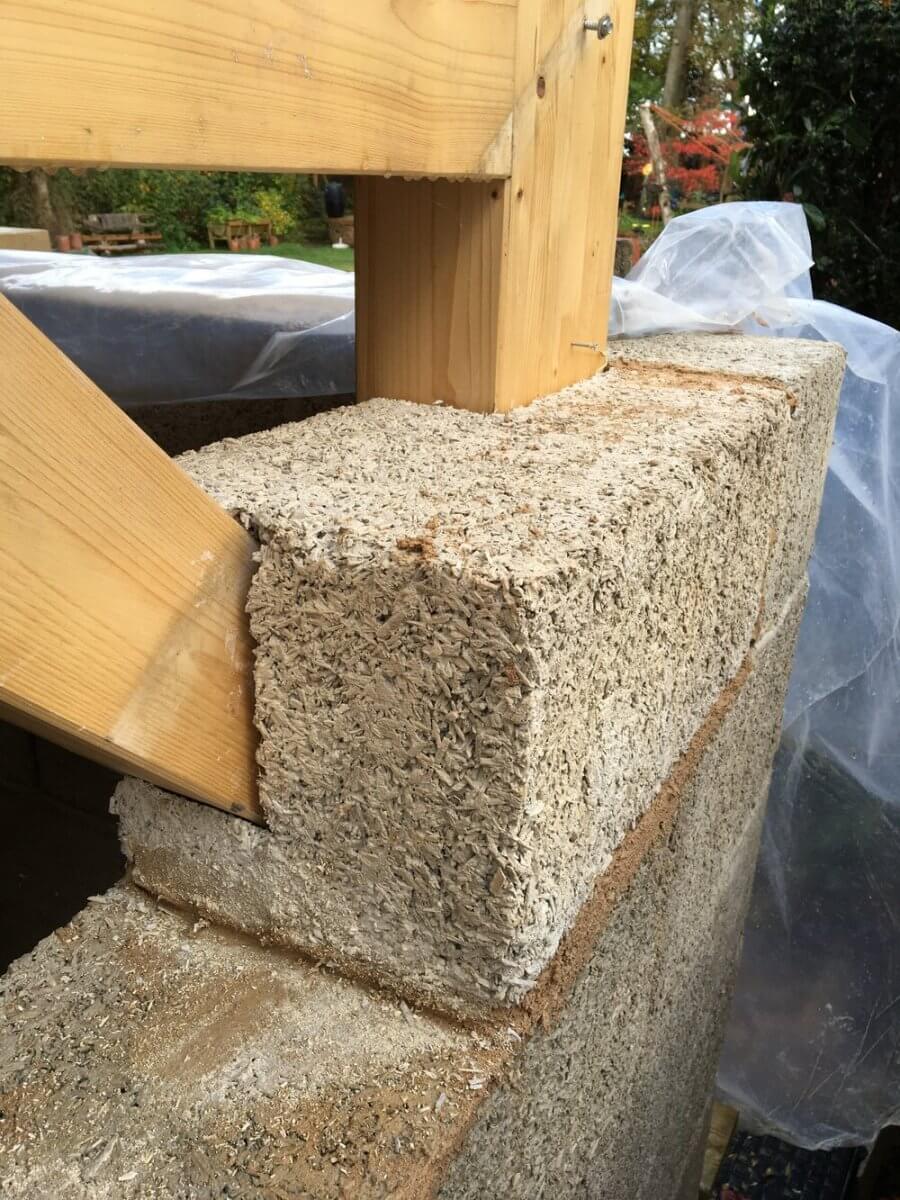
Many companies are racing to bring hempcrete blocks, bricks, and panels to market. Some see it as a kind of holy grail of mass-produced, industrialized, and affordable hemp housing. Bricks can be freighted to the site and laid by masons with a lime-based mortar. This method is still in its infancy and great attention must be taken to detailing because bricks cannot shroud the frame as spray-applied or formed hempcrete. With air gaps around the timber frame, the opportunity for cold bridging can occur, causing loss to the insulative abilities of the wall.
Which Method Would Work Best for Me?
Some prefer the sharp lines and modern look of hand-placed shuttered walls. Others prefer the rounded and blended look of sprayed hempcrete. There is a fair amount of crossover I would say, and you can achieve modern and classic styles employing either of these methods. In terms of efficiency and quality, some say spraying is quicker. Others say spraying is too messy because you have about 15% that doesn’t make it onto the wall. Still, others say hand-placing can be limited. Both methods have their pros and cons, and the jury is out as to which will eventually come out on the top as the future industry standard.
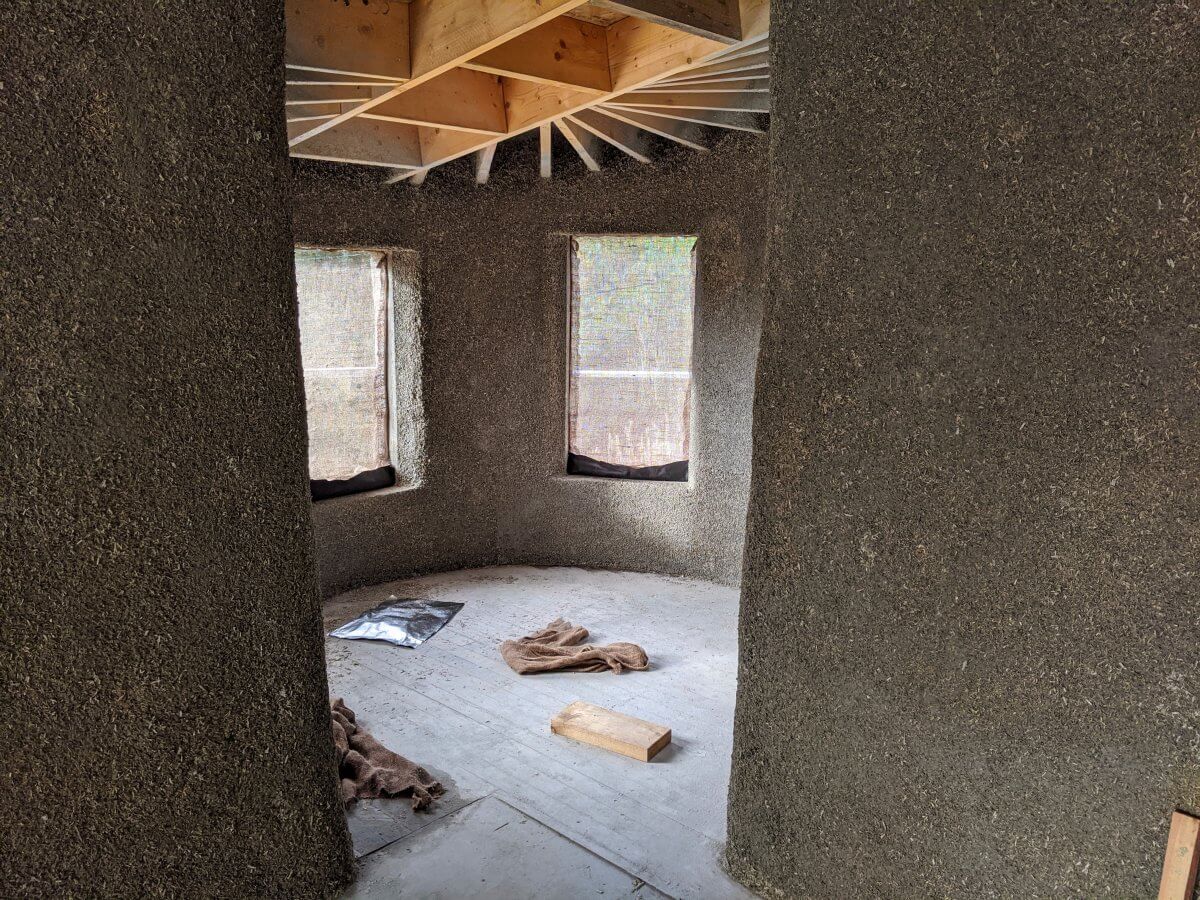
When you add up all the benefits of hempcrete: health and respiratory, environmental, energy savings, safeguarding against rodents, rot, molt, and termites; and the actual comfort factor of a finished hempcrete house, you find it hard to argue against the fact you’ll be seeing a whole lot more of hempcrete in the future.
Will Brain is a hempcreter based in Melbourne, Australia. You can find more of his writings and documentation of his work as a contractor at www.brainbuilt.com.au
Thanks for the article Will.
A few notes:
Name of original chaux et chanvre genius = Charles Rassetti
Another term for hempcrete = hemp-lime
It “never rots” if it doesn’t stay permanently wet and is allowed to dry out
The recarbonation of lime is called the lime cycle
Another method for building walls other than slip-forming and spraying is factory panel and infill, which won’t have air gaps in it – see http://www.calmura.ca
Definitely looking forward to many more hemp-lime, or monolithic biocomposite buildings in the future!!
Great article, thanks!
I would be intensely curious to know if anyone has tried yet to marry hempcrete (or hemp lime) with the monolithic dome building plans or technique?
I am trying to find someone who makes the Hemp bricks and if not then the other. Also looking for people to make clothing or sell clothing. Is this something you can help me with?